Let's recapitulate what we have seen in the previous articles:
Lead-acid batteries | Lithium batteries |
---|---|
|
|
Lead-acid batteries love to remain fully charged indefinitely but hate to cycle and stay for any time in a discharged state. Lithium batteries however hate to remain charged but love to cycle and to remain forever in a discharged state. It is almost as if they are made to complement each other.

A Lithium Hybrid system is a system where you don't replace your lead-acid batteries but just add a BMS-equipped Lithium battery to an existing lead-acid based installation.
How this compares to other lithium implementations you can read in our article lithium implementations.
How can it work?
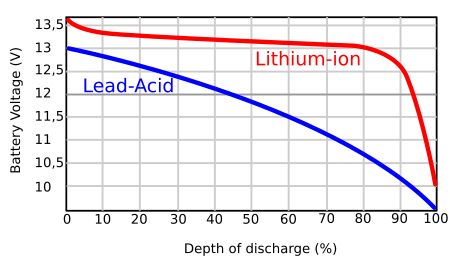
Operating the lithium batteries and lead-acid batteries in parallel is possible because lithium batteries have a much flatter charge and discharge voltage curve.
Discharging
While discharging, the lithium batteries stay above 13.0 Volt until they are almost empty. The lithium voltage is higher than the voltage of a lead-acid batttery under load, so the lead-acid battery will hardly deliver any current, if anything at all.
After the lithium battery has only about 20% of charge left the voltage becomes low enough to allow the lead-acid batteries to gradually start taking over the load. Only when the lithium battery becomes fully discharged and is taken offline by the BMS, the lead-acid batteries will fully take over. With a correctly dimensioned lithium battery, this will only happen in rare situations. Most of the time, the lead-acid batteries will remain fully charged, which is exactly what keeps them healthy.
Charging
While charging, the voltage quickly rises to about 13.4 Volt, a voltage where the lithium batteries absorb all the available current but a too low voltage for lead-acid batteries to meaningfully charge. So the lithium batteries take up all the current until the BMS takes them offline, and only then the voltage rises enough to charge the lead-acid batteries.
When charging the lithium battery, the chargers "see" a voltage which is similar to the voltage of a lead-acid battery which is in its early bulk phase, so the chargers are providing charge current to the lithium battery while "thinking" they are charging a normal lead-acid battery, patiently waiting for the voltage to increase.
When the lithium battery is fully charged it is taken offline by the BMS, the charging continues with the lead-acid batteries only, following a charge trajectory which the chargers fully recognize, allowing them to do their "end-point-voltage-limiting" thing. If the lead-acid battery has not been used, the voltage will rise quickly to the end-voltage and the charge process will be terminated and revert to a "float" voltage.
As long as there is a charge current available the fully charged lithium battery will remain "parked" aside and the on-board equipment will be fed by the charge sources with the lead-acid battery as a buffer. Only when the lead-acid voltage starts dropping below the float voltage, indicating the absence of a charge source, the BMS will put the lithium battery online again.
Note that OpenHybridBMS implements a "lead-acid priority" feature, where after a (partial) discharge of the lead-acid battery, the lithium battery is held offline to allow the lead-acid battery to first complete its bulk charge phase, then to charge the lithium battery, and then to use the remaining available charge current to finish the lead-acid absorption phase.
In practice
So the lead-acid batteries don't disturb the lithium batteries at all. The lead-acid batteries don't have to be "regulated", they just remain connected to the DC-bus all the time. The whole system works naturally, the BMS only has to disconnect the lithium battery to prevent it from overcharging and overdischarging. Practically, the lithium system is just a simple add-on to an existing unmodified lead-acid installation and is the most easy conversion you can imagine.
In a hybrid lithium/lead-acid installation you are going to use the lithium batteries to cover the short time (i.e. overnight) cycles. The lithium cells discharge deep enough to keep them healthy and the lead-acid batteries are just doing nothing at all, just sitting there fully charged the majority of the time, which keeps them healthy as well. Only when there are multiple days without any means of recharging, which usually does not happen very frequently, the lead-acid batteries are used to supply their reserve power after the lithium batteries become fully discharged.
The big advantages of a Hybrid installation
- Simplicity
- You don’t have to change anything on the ship to convert to a hybrid installation. You can continue to use the existing alternators, wind generators, solar controllers, etc. You don't have to split the DC-bus into a dual-bus with a "chargers" and "dischargers" branch. The lead-acid batteries remain connected to the power bus all the time, just as before. The lithium batteries are controlled by their BMS which can take them offline whenever it likes to, because the alternators then still "see" the lead-acid batteries which they were designed for. This is the only way to correctly use Lithium power on a ship without redesigning the entire existing installation.
- Redundancy
- You have a plan B. If something fails with the lithium battery or its BMS, one has still the unmodified lead-acid system to automatically fall back to. Sure, lithium batteries are very reliable if treated well, but they can not work without a BMS, which comprises of complex electronics and is sensitive to salt water, lightning discharges, connectors, sensors, corrosion, etc. If things go wrong, nothing beats the simplicity of a lead-acid battery.
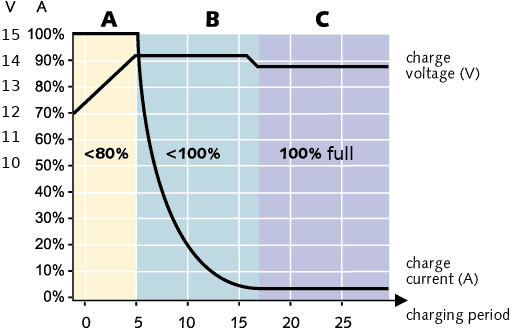
The trajectory under A is called "bulk phase", B is called "absorption phase".
- Optimisation of charge time
- The problem with lead-acid battteries is that they rarely accept the full available charge current after they are charged above 80%. The current tapers off and to get them close to 100% charged means hours of charging, despite the high output alternator you might have installed. But with a hybrid system you usually only used power from the lithium battery so only the lithium battery needs to be recharged, and they accept the full available charge current right up to the moment they are fully charged. This means that the charge time remains as short as possible. Finally you see the full rated output of your alternator flowing into the battery, right up to the end.
- Longevity
- Both the Lithium batteries and lead-acid batteries are enjoying a maximum life time because they are operating in a way that suits them best: The lithium batteries are cycled daily and don’t have to spend much time in a highly charged state, the lead-acid batteries are rarely cycled and spend most of their time being fully charged.
- Economical
- Because of the stretched longevity of both batteries in a hybrid installation, it is the most economic configuration possible. Also, installation wise, it is the most economic as no major modifications of the wiring need to take place and no charge sources have to be replaced or modified.
- Maintainability
- The ship will continue to use standard alternators and other chargers, with standard replacement parts commonly available, with no ties to a specific brand. No dual bus topology is used, a topology which would likely be confusing to engineers unknown with the lithium technology. This system is understood by engineers all over the world and can be serviced just like a regular system.